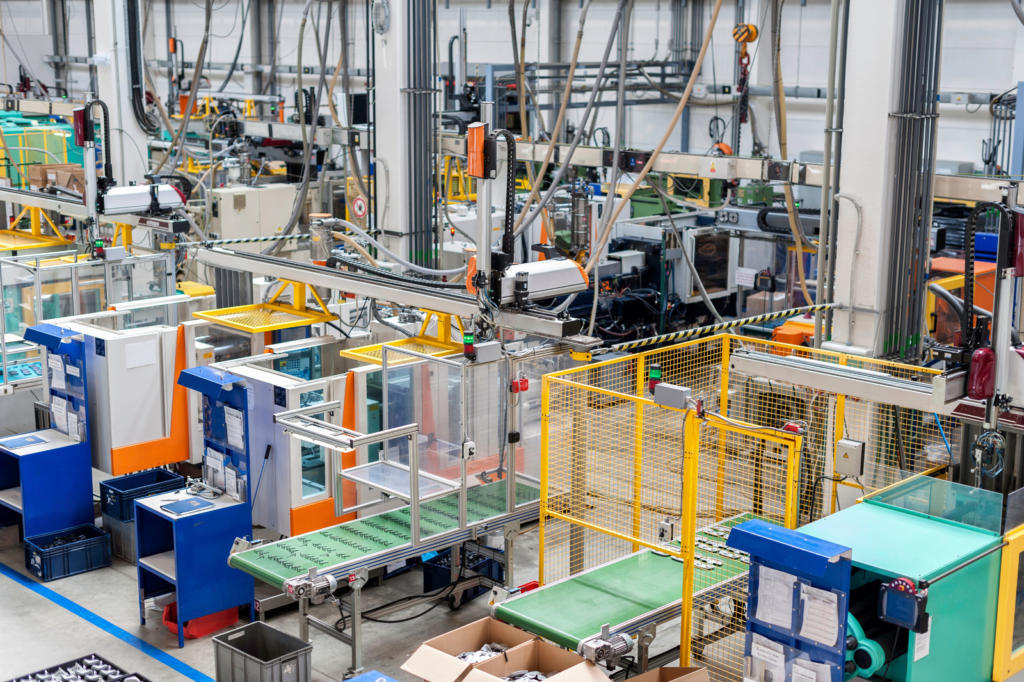
How to prepare for when your test team starts to retire
The skills gap and workforce reduction in US-based manufacturing jobs has been around for years.
This situation was accelerated by the SAR-CoV-2 pandemic, with baby boomers retiring at faster rates, and the supply chain issues of 2021-2022 are motivating US manufacturers to boost manufacturing by either re-shoring or rethinking plans to off-shore.
A 2021 study by Deloitte (https://www2.deloitte.com/us/en/insights/industry/manufacturing/manufacturing-industry-diversity.html) identified that 2.1 million manufacturing jobs may go unfilled by 2030. One of the main causes is baby boomers aging out and retiring. Another survey from the U.S. Census Bureau (https://www.census.gov/content/dam/Census/library/publications/2020/demo/p25-1144.pdf ) says it’s expected that by 2030:
- 1 in 5 Americans will be 65 years or older
- and the number of people under 18 will be nearly equal to those 65 and older.
If manufacturing output is going to improve in the US in the near future, manufacturers will need to do two things:
- do a better job hiring
- improve the effectiveness of those hires.
We ran a survey on LinkedIn and an overwhelming number (85%) of respondents identified training replacement test engineers as the most popular means to handle the aging-out of soon-to-retire test engineers.
Yet, any new test engineer will almost certainly have different backgrounds, desires, and skills than those soon retiring. So, besides a quantity gap, there will be skills gaps, or at least differences, that will need to be addressed.
Only a couple scenarios exist:
- If the manufacturing company already has replacement engineers on staff targeted to replace the soon-to-be retirees, preparation and training will be needed.
- If no replacement engineers are available, the manufacturer will either need to hire, partner with a test system integrator, or both.
This article explores some details around these paths.
For simplicity, let’s call the retiring test engineer Robert (the Retiree) and the new test engineer Nicole (the Newcomer).
Getting ready for your experienced engineers to start to ramp down
For either path(s) chosen, the following steps should be taken while Robert is still around:
Making sure the necessary docs exist and are up-to-date
The tribal knowledge in Robert’s head needs to be written down.
It’s so important to have this reference material available for Nicole when Robert does retire. Unless Robert and Nicole can work in an apprentice-like situation for years, Nicole will one day stumble on an unknown issue. Without the documentation, Nicole will have to reverse engineer the situation – which could be a huge source of wasted time and risk.
Also, have Robert review existing docs for any changes (e.g., redlines) that might not have made it into a final version. Out-of-date documents will lead to reverse engineering and possibly mistakes, making them possibly even worse sources of inefficiency and risk that Nicole would have to handle.
Some likely documents to create / update include:
- Mechanical drawings of the test system chassis hardware
- Electrical schematics of the test system wiring and component connections
- Bill of materials
- Software architecture for a high-level overview of how the software functions
- Test system requirements
- Test system acceptance plan
- Test procedure
- Names and roles for people involved in the design, build, and maintenance of the test equipment
Updating the tech refresh plan or creating if none exists
Robert likely has in mind (i.e., unwritten) some ideas about how to upgrade and/or maintain the existing test equipment.
Document these ideas because it’s very likely that Nicole’s next big project will be an obsolescence upgrade. Some idea can be found in this Tech refresh plan checklist for updating obsolete automated test systems.
Identify critical spare parts
Similarly, Robert likely knows parts or components of the test system that are becoming obsolete. Having spare parts in inventory will help Nicole manage test system downtime.
Pinpoint opportunities to reduce resource needs
Consider methods and tools to reduce the amount of time and effort needed for a test engineer to support existing test systems and develop new ones. Some areas of consideration are:
- Automating tasks to reduce effort. Some examples are:
- A diagnostic tool to test the test system in case of system nonconformance
- A calibration tool to aid in periodic sensor and/or I/O calibrations
- A deployment tool for upgrading test application software and/or configuration files
- Standardizing test system applications and system designs to simplify support and new development. It’s hard to maintain and improve a myriad of applications built on different code bases. However, complete standardization generally doesn’t make sense either (see An argument against universal test equipment). The best approach will identify the apps that are most critical to operations and diagnose them to see if it’s worth the effort to rewrite them to modern programming standards and with a common code base (see How to deal with LabVIEW spaghetti code). Experience shows that most manufacturers make similar types of products that can be tested with similar (i.e., configurable) test steps, whereas past approaches were likely purpose-built for each type of product.
- Partnering with an outside Test System Integration firm. Good test system integrator companies have experience that can fill resource and schedule gaps as well as provide technical know-how from which Nicole can learn.
Each manufacturer will have additional areas to consider. With digital technologies and new software development tools available, Nicole should be able to support more test stations than Robert could handle 10 years ago. However, in all likelihood, an investment in effort will need to be made before the company will see an improvement in Nicole’s efficiency. One method to manage this investment might use the concept of a “J Curve” (https://en.wikipedia.org/wiki/J_curve) which is often applied to the ROI on company projects and could also be applied for test project.
Attracting and retaining new test engineers
Attracting
If Nicole is not yet an employee at your company, the first hurdle will be hiring.
The stigma of working for a manufacturing company seems to be waning for young engineers.
Yet, as re-shoring continues and companies are looking to limit supply chain issues, the National Association of Manufacturers is projecting a 2.1 million job deficit in manufacturing facilities based in the U.S. by 2030.
That deficit presents an opportunity for engineers interested in manufacturing jobs.
Engineers looking for work in manufacturing have less need for a college degree than in the recent past. Vocational and community colleges have responded to manufacturers, which are requesting access to more students, by tailoring courses and instruction for using increasingly complex and computer-controlled manufacturing equipment.
Thus, any manufacturer seeking a new hire should engage in events at local vocational and community colleges in addition to such events at local or national colleges and universities.
Manufacturers should identify attributes and projects likely to be attractive to the “always connected” and tech savvy younger people.
The younger generation of engineers are not afraid to fail and expect to take on tasks which allow them to try new things and adjust as needed (see https://inductiveautomation.com/resources/podcast/educating-the-next-generation-of-manufacturing-engineers#:~:text=Fail%20quickly%2C%20learn%20quickly%2C%20change%20quickly.). For any manufacturing industry that recognizes the speed at which digital transformations are taking place (or should if staying competitive), creating a work environment suited to this “fail, learn, and change quickly” mode will be very attractive.
The traditional work/life balance of manufacturing will need to address the desires (see https://www2.deloitte.com/us/en/insights/industry/manufacturing/manufacturing-industry-diversity.html#:~:text=work/life%20balance.-,Work/life%20balance,-%3A%20Expectations%20and%20reality) of the new younger talent to be more balanced than in the past.
And, having more diversity in new hires will be attractive.
These job attributes are cultural in nature, which are almost always hard to change, but so important to attract younger engineers.
As for the types of test system projects that would likely be interesting to Nicole, some examples listed below are based on the fact that younger engineers are comfortable in, and savvy about, the digital world:
- Additional automation to extract more efficiency and value from test systems, including remote maintenance and troubleshooting.
- Industry 4.0 for operations and quality improvements to collect, share, and analyze data from test systems for the benefit of operations.
- Data analytics and data engineering to process, correlate, and present test system data.
- Integrating cloud-based tools and analytics to spread the use of data collected across a plant and even worldwide if the manufacturer has that footprint.
- Develop and deploy both better user interfaces and tools, including augmented reality tools, to assist and enhance assembly and test operators. These “Augmented Lean” tools (see https://www.augmentedlean.com/) are often the next step for assembly and test frontline workers.
These and other initiatives are part of the cultural and digital transformation many companies have decided should be a part of their strategy. This strategy will be exciting to new test engineers, like Nicole, so companies must be open to the changes in order to hire Nicole and others.
Upskilling
While the previous section dealt with hiring new test engineers, don’t forget to consider bringing an existing younger employee into the position. Many of the recommendations given above apply here too. Yet one important difference is that upskilling considers changing a talent management approach from a “supply chain” of static job descriptions to defined linear career paths.
This way of treating job roles (see https://www2.deloitte.com/us/en/insights/industry/manufacturing/manufacturing-industry-diversity.html/ ) can be important to younger engineers.
Retaining
Retaining new test engineers, regardless of being a new hire or an existing employee, requires engaging them in their jobs.
One survey (see https://www.zippia.com/senior-electrical-engineer-jobs/demographics/#:~:text=The%20Average%20Number%20of%20Years%20That%20Senior%20Electrical%20Engineer%20Stay%20in%20a%20Job ) shows that electrical engineers stay in the same job an average about 6 years, while the average for software engineers at Google (see https://www.cnbc.com/2019/12/03/a-tech-firm-tried-it-all-to-stop-turnover-only-one-thing-worked.html#:~:text=The%20median%20tenure%20on%20Google%E2%80%99s%20team%20is%201.1%20years%2C%20according%20to%20PayScale ) is 1.1 years according to another survey. Smaller engineering firms have longer tenures of 10+ years (see https://johnsonengineering.com/careers/#:~:text=average%20tenure%20of%2013%20years). Even at 10+ years, it’s costly to lose and then rehire an engineer who has received training and mentorship to become a productive contributor.
Some tips to help retain test engineers:
- Encourage involvement in test-centric events, such as in-person and online conferences.
- Have them get involved with introducing manufacturing opportunities to students at all types of schools, such as vocational, community, and 4-year colleges.
- Urge participation in groups aimed at fostering engineering careers in manufacturing.
- Form teams with other test engineers to solve problems as a group.
- Utilize and support online training to stay abreast and learn new methods and tools.
These tips are aimed at engaging test engineers, building a community to enhance their knowledge and support base, while encouraging them to grow technically.
Training new test engineers
Getting Nicole up to speed as a test engineer focuses on training on general topics about testing and specific topics related to existing test stations.
If Nicole is new to test, some general training topics include:
- Familiarizing and building capability in the programming language(s) used to automate the test systems.
- For example, if LabVIEW is the primary language, online training classes are available at https://learn.ni.com/.
- Based on the growing interest of Python and C# as important programming languages, training courses in Python (see https://www.coursera.org/specializations/python-3-programming )and C# (see https://dotnet.microsoft.com/en-us/learn/csharp ) abound (these links are just one of many online classes).
- If programming is a completely new area, take some courses in programming methods.
- Become familiar with the types of test hardware and their communications protocols used in the test systems.
- Some good starting points for data acquisition:
- are found at NI (see https://www.ni.com/en-us/shop/data-acquisition/sensor-fundamentals–data-acquisition-basics-and-terminology.html)
- Measurement Computing (see https://www.mccdaq.com/data-acquisition).
- Introductions to communications abound on the internet. Some nice overviews for basic serial comms:
- Introductions to ethernet-based comms, such as OPC and EtherCAT, are also abundant and can be found at communication vendors, such as https://www.rtautomation.com/technologies/ethernetip/ and even specific product web pages such as https://www.encoder.com/hubfs/white-papers/WP-2019_Industrial-Ethernet-Protocols/wp2019-industrial-ethernet-communication-protocols.pdf .
- Some good starting points for data acquisition:
The next step would be to have Nicole work with knowledgeable test engineers. Robert would be ideal if he’s still an employee. This arrangement could be structured as an apprenticeship of sorts, where Nicole shadows and is trained by Robert for an extended period.
In larger companies, Robert might be part of a larger team that’s focused on test systems. While Nicole might be aimed at one or two specific test systems , she should spend some time to learn what the team is doing, specifically the status of all the test systems (operational, near obsolete, brand new, …) and their plans (no change, retrofit for new features, obsolescence upgrade, …). Being aware of the tasks and goals of all the people in the test system team will help encourage open dialog when help and mentorship is needed.
Another approach to training new test engineers is by engaging with an outside test system integrator company where Nicole learns by being engaged during the upgrade of an obsolete test system or build of a new one. Also consider that a test system integrator could be a resource for Nicole to discuss test topics and get recommendations.
Engaging with a test system integration company
Besides building the capability of internal staff, whether by training new skills with an existing engineer or by hiring new staff, it makes sense for a manufacturer to consider utilizing an experienced Test System Integration company.
There are pros and cons to consider with this arrangement. Ideal timing would be when Robert and Nicole are both onboard so that the test system integrator can assist with the transition before Robert retires.
Less ideal but still worthwhile would be to have the test system integrator work with Robert. This arrangement would aid in knowledge transfer.
Pros of working with a Test System Integrator
Some of the benefits of having a working relationship with a test system integrator center around their experience to help maintain, upgrade, and design and build new test systems.
- One-stop shops for both design and build: Test systems almost always go through some engineering give and take at the beginning of the project to meet schedule and budget. It’s usually most efficient to choose a single company that offers this style of consultation along with the design and build capabilities. Many test system integration companies focus on build-to-print and expect someone else to do the design work. Other test system integration companies have expertise in the test automation software but not the hardware needed to connect to the device under test. We recommend working with a test system integrator that can complete the entire project to maximize the utility of the test system integrator.
- Specific tech expertise: If the test system integrator has experience with specific technical parts of the test that you want, that test system integrator will clearly be more effective than if Nicole or Robert need to figure it out themselves.
- Project management experience: Some test system integrators have the engineering bench depth and financial management required to handle the project so you don’t have to do that work.
- Continuity: The employees at a test system integrator aren’t affected by employee promotions and transfers as much as at larger manufacturing companies. The test system integrator that delivered a test system even 15 years prior will likely still have access to the engineers who worked on that system.
- Manage the humps: Companies with an internal test engineering group can be overwhelmed occasionally, say by multiple simultaneous new product offerings. Having a relationship with a test system integrator can ease the burden by outsourcing the excess work.
- Consulting: you can tap into the test system integrator’s experience base by involving them with the design and consider having them provide project management for the build.
Cons of a test system integrator
Some of the cons for working with a test system integrator:
- They’re not available at a moment’s notice: Every test system integrator has a set of current and backlogged projects. It’s possible that they can accept your project into the workflow, but perhaps their workload is too large to accommodate your project. The best solution is to work with the test system integrator to figure out the ways they can assist in part rather than dismiss engaging them entirely.
- Remote vs local: a project that requires the test system integration engineer to be onsite at your location for months or years may be contrary to the test system integrator’s project process. However, don’t assume they can’t help. Rather check if they’re willing, and the extent of their onsite support.
- Engagement processes and paperwork: Bringing a test system integrator on-board requires some steps. For example, a requirements document should be developed to describe the project so the test system integrator can evaluate and make a proposal. And, the procurement department might need to set them up as a vendor before creating a purchase order. These steps will consume your resources.
Next Steps
If you’d like help during your test team’s transition, feel free to reach out for a chat.
If you’re thirsty for more info on this topic:
- Search for phrases such as “hiring to replace retiring “engineers”” or “training to replace retiring “engineers””. You’ll find dozens of good articles that augment this test-centric article.
- To learn more about handling the transition of test system engineers, a Deloitte article (https://www2.deloitte.com/us/en/insights/industry/manufacturing/manufacturing-industry-diversity.html ) and a McKinsey article (https://www.mckinsey.com/capabilities/mckinsey-digital/our-insights/tech-talent-tectonics-ten-new-realities-for-finding-keeping-and-developing-talent ) are excellent overviews about manufacturers and tech companies.
- For test-centric information, an article that overviews automated test systems and some general information about test systems may be useful.
- Make sure you have a tech-refresh plan for the eventual test system upgrade that Nicole will need to tackle.
Deep into learning mode? Check out these resources:
- Practical manufacturing test and assembly improvements with I4.0 digitalization
- What to do with your manufacturing test data after you collect it
- 5 Keys to Upgrading Obsolete Manufacturing Test Systems
- How Aerospace and Defense Manufacturers Can Make the Assembly and Test Process a Competitive Advantage
- 9 Considerations Before you Outsource your Custom Test Equipment Development
- Reduce Manufacturing Costs Report
- Improving Manufacturing Test Stations – Test Systems as Lean Manufacturing Enablers To Reduce Errors & Waste