Practical manufacturing test and assembly improvements with M4.0 digitalization
5 benefits of digitalization:
- WIP visibility
- Identifying sources of waste
- Station utilization and OEE
- Training and skills management
- Regulatory audit support
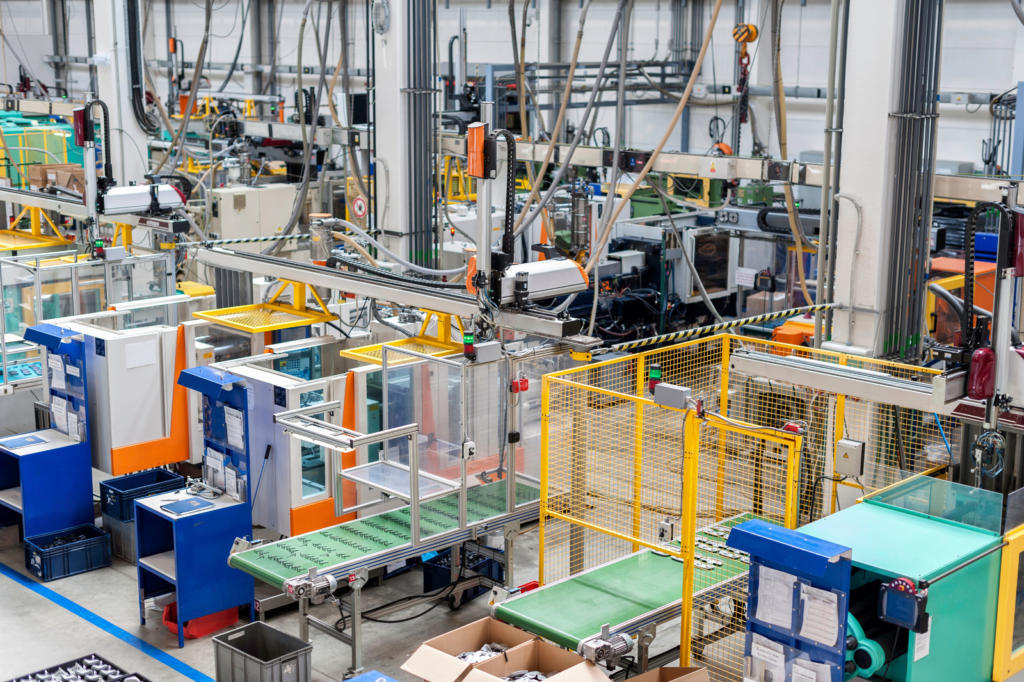
Discrete manufacturers continue to expand the automation and digitization of processes and data capture. Those with huge production volumes, such as automotive components, have a clear cost-saving reason to substantially digitize and automate along the lines of M4.0-driven strategies However, those with a high-mix and low-volume product mix can struggle to see how to achieve the necessary payback.
We’ll share some practical incremental steps to apply digitization and automation to help achieve M4.0 goals in discrete manufacturing.
Obtaining benefits (the payback) doesn’t require a wholesale deployment across the entire plant floor.
Incremental steps can and do work.
The goal of complete plant-wide digitalization can be approached in stages. In fact, there are benefits to taking small steps because you’ll learn a lot during the process.
Assembly & Test Stations – the opportunity
In discrete manufacturing, M4.0 initiatives are often based on 3 manufacturing elements:
- Lean,
- Digitization,
- Automation.
These 3 elements are required for digitalization which, as defined here, is the improving of processes by leveraging digital technologies and digitized data.
This article explains the benefits of assembly & test (A&T) system digitalization, and how these 3 bulleted elements can be applied incrementally.
In years past, companies were hesitant to use data from an A&T station to benefit Lean processes, thinking that collecting that data would be too costly and many years away. The payback was non-obvious, and Lean was working well enough for these A&T stations.
However, our experience shows incremental steps are achievable and benefits can be enjoyed in months. For example, one long-term client of Viewpoint Systems, a large aerospace manufacturer, started applying digitalization to a few A&T stations and showed benefits in around 6 months. Now, 10 years later, they have deployments worldwide.
Incremental steps are good for both learning as you go and for annual budgets.
Benefits of A&T Digitalization – the improvements you can realize
The 5 main benefits of digitalization include:
- WIP visibility
- Identifying sources of waste
- Station utilization and OEE
- Training and skills management
- Regulatory audit support
Improvement – WIP Visibility and Traceability
If each part has an ID, the A&T station can associate this ID with the A&T data, such as when the part arrived at the station, which station, and the exit time.
Once every A&T station pushes operational data to a central data store, queries can extract information about the location on the factory floor of any specific part based on that part ID. This gives visibility into the flow of products through the A&T operations, showing:
- bottlenecks,
- excessive inventory,
- and over- and under-used A&T machines.
Any need to review the manufacturing history of a particular part, including any rework, is satisfied by another query. These queries are often useful for handling warranty issues and when being audited by a regulatory agency.
Improvement – Identifying and Ranking Sources of Waste
From a Lean perspective, data collected into electronic records can be mined and analyzed for operational and unit performance issues.
Measurements of the A&T execution can be captured, such as:
- the takt time of the entire procedure and each individual step,
- failure mode and/or operator comments from each step,
- the operator involved,
- and the work instruction used.
Statistical analysis of this data boosts the utility of Lean procedures by helping to identify and rank sources of waste.
Also, manufacturing managers have access to WIP status and operations managers can identify areas and operators needing improvement and additional training.
For example, analyses of operational data will highlight bottlenecks by operator, A&T station, WI step, and by a part type (model). Unit performance outliers and failures can be ranked by step result to find which assembly steps are causing the most problems. Steps that result in failure can be cataloged by failure mode to identify the failures that need the most attention.
Without these electronic data sets, choosing where to focus improvement efforts is obviously going to be less efficient than recognizing and attacking the most prevalent issues first.
Improvement – Station Utilization and OEE
With insight into how parts flow through the manufacturing processes, additional understanding can be gathered into how the A&T stations are utilized and how they’re performing.
By reviewing the durations and the start times of all A&T procedures, an estimate of the amount of time a particular A&T station is active can be calculated. Bottlenecks identified in the “waste” queries can point to overused equipment, suggesting that an additional A&T might alleviate that bottleneck. Conversely, if a station is being underutilized, maybe it can be repurposed or retired.
This utilization calculation feeds into availability, one of the three components of overall equipment effectiveness (OEE): Availability, Performance, and Quality. As typically defined:
- Availability is the percentage of scheduled time that the station is active, a number that can be calculated from the A&T records.
- Performance is a measure of the number of parts per hour produced, as recorded at the A&T station, compared to expectations.
- Quality is usually defined as first pass yield, another number available from the A&T station records.
Improvement – Training and Skill Management
With a list of training histories for each operator, the test executive can limit operator access to those trained on specific electronic work instructions.
By using a test executive to automate walking through a work instruction, a novice operator can rely on the step-by-step nature of this execution to bolster earlier training.
Sometimes, training opportunities appear due to high turnover or new product introductions. In that case, the electronic work instruction contents can be broadened to include additional information useful for training. This additional info would only appear if the operator was designated as a trainee. By giving each operator an ID, the sequence execution application can use it to look up the operator’s training history. If an operator has not been trained on a specific work instruction, it either can be made inaccessible or can offer useful training material.
If operational metrics for one operator show more frequent issues and longer execution times, then there is a potential training opportunity to train this operator based on the actions of the other operators. Or, if the opposite, figure out why this one operator is performing better than others and train the rest on that operator’s techniques.
Improvement – Regulatory Audits and Version Control
Since the electronic work instructions are electronic, version control tools can bring organization and access rights to the versions of electronic work instructions used by an operator.
Often, prior product revisions are returned to the factory for maintenance and warranty. These prior revisions might have been assembled and tested with different steps than the latest version.
For example, circuit board Revision A might have a different set of test points than the most recent Revision D. When Revision A is being worked on, the operator can access the proper version work instruction for Revision A by selecting this electronic document from a list (or have the test executive automatically select the proper work instruction based on the part ID). A version control tool manages the development and release history of all the versions.
Coupling version control with operator access control in the test executive prevents untrained operators from having access to the wrong versions.
Regulatory audits usually check to assure that the operators know their jobs by checking training records for actual work performed. Controlling access to electronic work instructions according to the associated training closes this potential audit gap.
With detailed records of steps performed, parts worked on, and operators doing the work, the manufacturer can point an auditor to what was done and by whom. Were the right processes followed? Was the operator trained on that procedure? The auditors love direct access to electronical records produced at the A&T station.
How to make the A&T improvements – recommended methodology and building blocks
An operator at an A&T station typically starts with a work instruction, which lists the steps in the A&T process. Each step creates information, such as when the step was completed, any measurements made, and checks for pass/fail. When the work instruction is completed, the operator creates a record of the results.
We want to digitize and possibly automate information gathering.
Let’s explore three A&T activities:
- Work instruction,
- Step execution, and
- Recording results
while being mindful of the data consumed and produced to achieve the three M4.0 goals for digitalization: Lean, digitization, and automation.
The 4 changes you’ll want to make, and in this order, are:
- Common data format and metadata: the data recorded at any A&T station should follow a standard pattern coupled with flexible data description, such as XML or JSON. Also record any relevant operational conditions, i.e., things that might matter to the results, such as time of day and humidity. More is better if unsure. Such metadata can be very important because they supply context when interpreting the A&T results.
- Electronic work instructions: no more paper! Electronic work instructions can be version controlled, downloaded from one spot so only the proper version is used, and written to contain additional info for new operators.
- Automation of step execution: with automated step execution, procedure shortcuts are removed, and consistent processes are followed. It isn’t necessary to automate the entire assembly and test process (e.g., via a robot or automated machine). At a minimum, automation should include execution of the procedure, capturing of results, and recording the metadata.
- Electronic results: making all recorded data electronic results in faster and more accurate analyses, decision making, and report generation. Historical records can be searched for trends and audits.
Common format and metadata
It’s important for the data to be uniform and flexible. For example, all A&T stations could record common items such as:
- the ID of the part about to be assembled and tested,
- the name and version of the WI,
- the timestamps of events (e.g., start of a step),
- operator ID,
- A&T station ID, and
- operating conditions (e.g., shift number, temperature, power levels, …).
This information should be described in a common fashion that enables modification in the future without breaking access to earlier data.
XML, JSON, and other text-based descriptions offer enough flexibility for future-proofing without needing to design an entire data management edifice up-front. These text-based descriptions won’t break old data if elements are added or subtracted, so your data can morph as needed.
Data stored in databases should include summary data and pointers to original sources to encourage modularity and maintainability.
An up-front endeavor to identify and accommodate such common data will put you on the right path to applying analytics across your entire factory operations. These common items are often labeled as metadata. Metadata provides context when analyzing “out of process” events.
This same mentality should be applied to the results of each step included in the work instructions for the assembly and test procedure. A description of the step and associated results, or pointers to such results, should accommodate all the steps.
Electronic Documentation for Work Instructions
A work instructions document organizes the A&T process into a sequence of steps, each describing a small set of tasks. An electronic work instruction is a digitized version of a paper-based instruction manual.
The format of an electronic work instructions can be a PDF, HTML, XML, Word, scanned from existing documents, and so on.
An operator using electronic work instructions follows the same process as with paper work instructions. The creation and use of an electronic document, versus a paper-based version, is an incremental improvement effort.
Automation of Step Execution
The execution of the electronic work instructions can be digitized with a test executive to automatically present each step to the operator before moving to the next step.
Several companies offer test executives, such as the StepWise platform from Viewpoint Systems and TestStand from NI. The operator cannot walk through the electronic work instructions in arbitrary order and no steps can be skipped. This disciplined presentation promotes execution uniformity across operators and procedures.
Any results, such as measurements, verification pass/fail data, comments, and so on, can still be initially recorded onto a paper-based record, but eventually the results should be digitized into electroinic records.
Automation of the execution of work instructions via a test executive is an incremental improvement effort that builds on the work done converting WI documents to electronic format from paper.
Electronic Results
The next stage captures digitized data during electronic work instructions execution. The test executive collects step information after presenting each step in the electronic work instructions. A spectrum of automation options exists to digitize the results of each step.
At a minimum, any results previously manually written into a paper-based report will be entered into the test executive’s dialog box field(s) presented to the operator at the conclusion of each step. This minimum approach is an incremental improvement.
At a maximum, the test executive and the equipment at the A&T station automatically perform the A&T steps. Sometimes, the operator is responsible for loading and unloading the unit(s). Other times, the A&T station has full automation with a machine loading and unloading units, a situation usually applicable to very high-volume manufacturing.
In high-mix, low volume manufacturing, the steps are usually a mix of these two extremes, with each step being automated to whatever level makes sense from a quality and financial standpoint.
Upon completion of the electronic work instructions, the test executive will corral all the results and send them to an electronic results file, such as a JSON text file, an Excel file, or a database. The format and structure of these results should follow the recommendations about common and flexible data.
Note that the amount and type of information being saved in an electronic record can initially be limited to the details most relevant to your purposes.
For example:
- if you suspect that a subassembly from one of your suppliers is causing issues, capture supplier IDs.
- Or, if First Pass Yield is low, gather measurements on unit performance and create a Pareto chart to attack the most prevalent.
- If a particular unit is “out of process”, a recommended practice is to have that product’s manufacturing engineer include in the unit’s metadata a “best guess” at the root cause.
It’s harder to diagnosis a cause when only the symptoms (i.e., measurements) are available and the context and possible reasons are not also recorded.
This stage of the digitalization ranges most widely from minimally automated solution of recording the results to a full-on automation where the A&T station does all the steps and data recording automatically. Thus, this stage can begin as an incremental effort and grow as payback makes sense financially.
Next Steps
We’ve discussed 3 goals towards M4.0 digitalization efforts on Assembly and Test stations:
- Electronic work instructions
- Automation of assembly and test procedures, and
- Collecting data into electronic results files.
Each of these goals can be incrementally approached, permitting access to benefits within months of initial efforts, while providing a known path to continual improvement.
If you’d like help making incremental progress in these areas, feel free to reach out for a conversation.