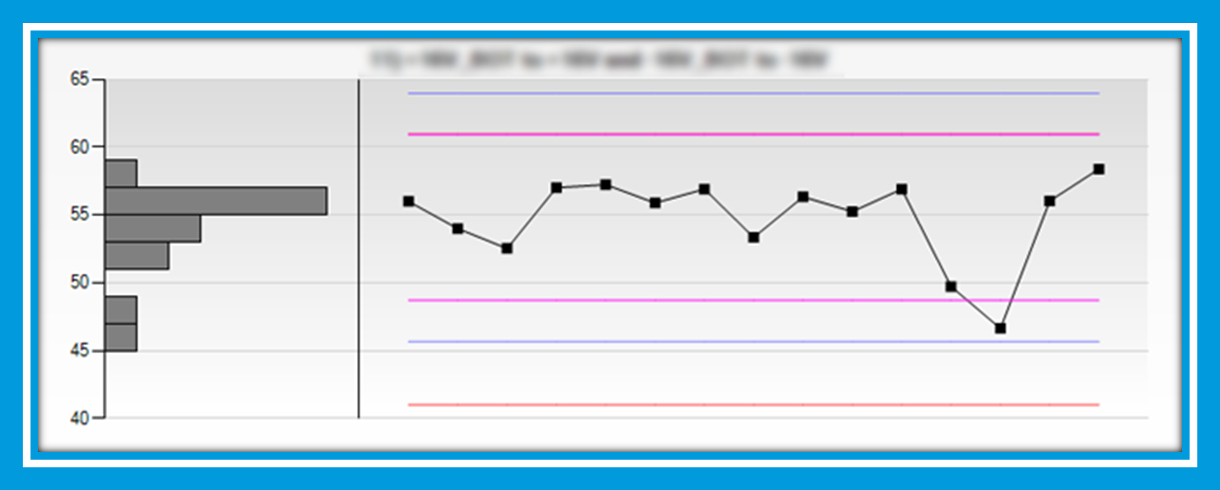
Integration of Data from Test and Business Systems
The test system mimics the earlier paper-based process to provide test operators with a familiar environment
Background
Many companies produce parts with high-complexity, in low-quantity, or both. These parts are often tested manually with test results captured on paper or in data files local to a test machine. Yes, even in this age of automation, some companies still pursue this approach because they believe the cost of implementing an automated test system is too high. Furthermore, they believe the effort of training the production team to use automation will be a challenge.
Motivation
However, companies that embrace electronic records and replace the paper can gain real benefits. By combining electronic test results from the testers with information on work orders and manufacturing flow from the business systems, we have seen marked improvements in manufacturing efficiency in low-volume, high-mix product companies, such as aerospace parts suppliers, medical device manufacturers, and electronic assemblies. We have combined business systems data into the test system via assembly instructions, test records, and production status. The test system mimics the earlier paper-based process to provide test operators with a familiar environment.
Challenges
Manual Processes
Many low-volume manufactures manage production by traditional means, with paperwork assigned to each production unit and operators performing inspection of the unit during manual assembly. Manufacturing results are reviewed periodically via a tally of production volume at each assembly station and issues encountered during assembly.
Paperwork
Assembly work instructions and resulting test data are written on paper that travels with each unit. As tests are performed, resulting measurement data were recorded manually. The chance for error is significant. Because of the need to review physical paperwork, significant labor can be involved in maintaining current information on production status. And, when questions arise about the status of a particular unit, many hours can be spent in locating and evaluating the paperwork.
Solution
Test Executive
A test executive (TE) is critical to achieving improvements, since both input work instructions (i.e., test sequences) and test results are now managed in electronic forms. These forms can be combined with data from the manufacturing business systems which contain information pertinent to production. For example, business systems often contain work orders, bills of material (BOMs), status of Work In Progress (WIP), and so on.
For our clients, we offer a TE called StepWise that offers user-configurable graphical operator instructions (created from the work instructions), automatic data entry, failure mode collection/analysis, and timing of each production step. In addition, the test sequences and test results are associated with unique identifiers for the part, operator, test station, and work order.
Test sequences are edited from pre-built test step types, such as “Read Voltage”, “Manual Measurement” and “Notes”, so that the client can create their own assembly and test procedures without engaging Viewpoint to support new products or to adjust existing work instructions. Furthermore, access to test sequences can be restricted by user privileges, controlling access to sequence execution, creation, and validation procedures.
Databases
We store the details of each production step into a NoSQL-style database based on the framework Aperio. This type of database is super-flexible and easily accommodates changes in the collection of parameters associated with the production data. This flexibility enables our clients to handle product design changes that require gathering of additional or fewer test data. Aperio offers trend graphs for SPC data for range charts, Cpk, and so on.
Summaries of the test data are available to be pushed into the manufacturing business database, typically a SQL-based Manufacturing Execution System (MES). For example, the test system gathers information on the time it takes to assemble each part, any failure modes, the status of any rework, and so on. After pushing this information into the business database, queries can produce reports on production performance, such as Work In Progress (WIP) and Overall Equipment Effectiveness (OEE) for the production test equipment. With these reports, the manufacturer can realize where improvements are needed and which improvements will have the most effect in quality, cost, and time changes. For example, production decisions are impacted by knowing which failure modes occur most often for each part type. Further, the WIP and test time information improves the ability to detect production blockages and alleviate them by assigning personnel to the bottlenecked assembly locations.
Summary
By combining business database information with electronic records produced from test and assembly results, manufactures can identify the most effective production improvements at the business level. We have seen clients that have reduced production costs by over 30% by embracing the integration of test and business data. Check out our production cost reduction report to learn more.