Manufacturing Test Data Logger
Data Acquisition System Facilitates Continuous Improvement of Product Performance
Client – A manufacturer of welding consumables
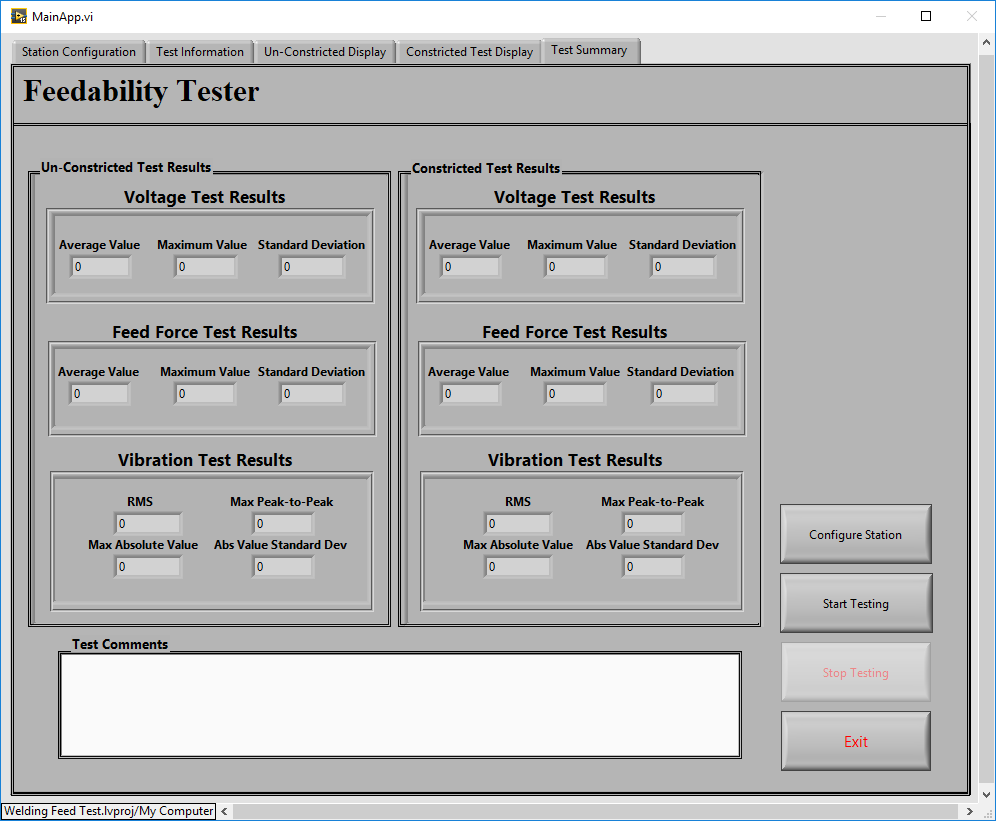
Challenge
Our client produces welding consumables. These products are inspected for continuous improvement of product performance. Our client wanted to standardize their data collection method to improve product quality and utilize SPC (statistical process control) across multiple international manufacturing facilities.
Solution
The solution is a relatively straightforward data acquisition system measuring force, vibration and voltage for comparison across multiple international manufacturing facilities to support continuous improvement of product performance.
Benefits
- Standardization of data collection across multiple manufacturing sites
- Ability to check product performance tolerances, which could trigger root cause analysis
- Ability to analyze data across product runs and across sites for SPC
System Overview
The system utilizes off-the-shelf data acquisition hardware from National Instruments along with custom LabVIEW code to perform force and vibration measurement and basic calculations such as RMS Min and Max. Each test generates an MS Word file showing summary data as well as graphs of each attribute over time. In addition, the program creates (and automatically archives) a complete data set of all data recorded during the trial and finally adds a line with all the summary results and comments to a Master log file. This Master log file can then be sorted by date, wire type, diameter, or any other input for analysis.
SOFTWARE FUNCTIONS |
---|
Calculations (e.g. standard deviation, RMS, Max) |
GUI for configuration, control, and results. |
Automated Report Generation |
HARDWARE USED |
---|
NI cDAQ |
NI C Series voltage input module |
NI USB Multifunction I/O Device |
INTERFACES / PROTOCOLS |
---|
USB |