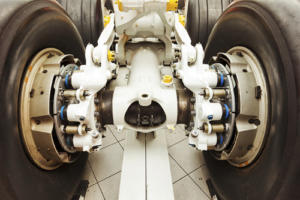
Decreasing Test Time for Aircraft Landing Gear
Endurance Testing for Aircraft Nose Landing Gear Steering
Client: A major manufacturer of aircraft landing systems
Challenge
A major manufacturer of aircraft landing equipment needed to develop a means of endurance and fatigue testing new designs for aircraft steering. The actuators involved in steering the nose landing gear (NLG) required precise and reliable control through thousands of steering cycles.
Control loops needed to be closed at faster than 1 ms.
Prior systems were handled manually without real-time control and monitoring.
Solution
Our customer designed and built a test rig to provide the hydraulics and environmental conditions for the endurance testing on the NLG. Viewpoint Systems supplied the electronic data acquisition and control hardware coupled with real-time software to provide the required fast control loops. The configuration and execution of the 1000s of steering cycles were managed by the same data acquisition and control system through a set of configuration screens that allowed specification of turn rates, min/max angles, drive and resistive torque settings, and so on. The flexibility offered with this HIL test capability mimicked the variety of conditions that the NLG would encounter in actual use.
- The various PID control loop configurations were also configurable along with gain scheduling required under different operating conditions.
- The environmental conditions were supported by controlling a temperature chamber through ramp and soak settings occurring during the steering tests.
- Measurements on the steering performance were collected from commanded setpoints, sensor readings, and controller outputs during the entire test run.
- Alarm and fault conditions, such as force exceedance, were monitored continuously during operation so that the system could safely run unattended.
Since the deployed solution was an aerospace test system, the entire system underwent an extremely rigorous acceptance testing procedure to verify proper and safe operation.
SOFTWARE FUNCTIONS |
---|
Arbitrary Load and Position Profiles |
Flight Position Control |
Load Position/Force Control |
Endurance/Flight Schedule Execution |
Deterministic RT for DAQ and PID Control |
HARDWARE |
---|
PXI/SCXI Hybrid RT Chassis |
Discrete Pump Skid Interface |
Custom Control Panel/Console |
INTERFACES |
---|
Ethernet TCP/IP |
SCXI |
Results
Prior to deployment of our system, setup of a test was much more manual and operators needed to be around to monitor operation.
With our new system, complete endurance testing could be specified and executed with minimal supervision. Furthermore, the tight integration of real-time control, HIL testing, and coordinated data collection made report creation much simpler than before.
The rigorous acceptance test gave trustworthiness to the data and allowed the design engineers to validate performance more quickly than the prior semi-automatic and manual methods of operation.
Setup of tests has been improved from prior operations. The endurance testing itself operated over a huge number of cycles lasting weeks to months between scheduled lubrication and maintenance.
The deployed system measures performance during the entire testing, even between the scheduled downtime.