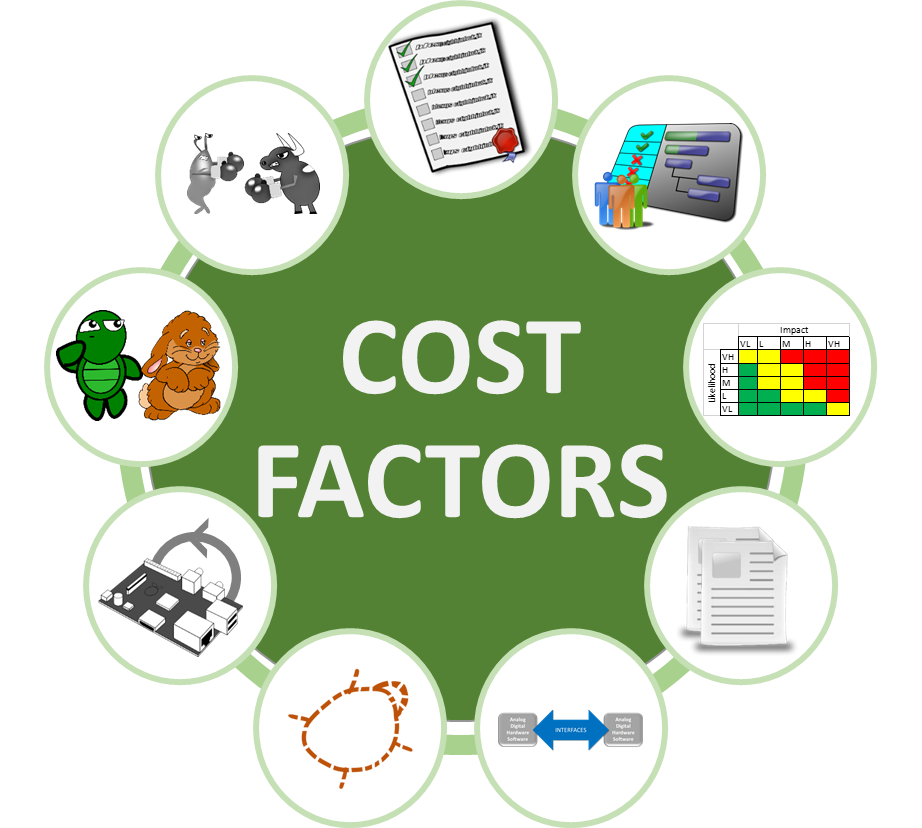
Designing An Industrial Embedded Controller – Important Costs To Consider – Part 1
Estimates for engineering development costs are challenging, and I mean really challenging
The emphasis of this article is on the prototyping of the industrial embedded controller.
When I say “embedded controller” in this context, it doesn’t mean that it actually has to control anything (it could, but isn’t required), but it will most likely have outputs. It could simply be monitoring signals to convey useful information to another piece of the system or system of systems.
This article is geared toward companies in the industrial world (vs consumer), that manufacture systems or sub-systems (machines, equipment) that are generally on the more expensive side (~$4,000 – $200,000 per system), and have lower production volume (10 – 1,000 units per year).
What is out of scope for this discussion?
- The front end research: in other words, an idea already exists, but it hasn’t been prototyped or proven out yet, or if it has, it’s been a lab-equipment-based proof-of-concept hack job.
- Manufacturing costs: while production volume should absolutely be taken into consideration for off-the-shelf vs custom component selection, I won’t focus on the manufacturing end of the product development process; rather I’ll focus on the development costs. Of course, designing with production in mind (not just volumes, but DFA& DFM as well) is still critical.
- The post-production maintenance, obsolescence, and customer support aspects are not part of this discussion.
The industrial embedded development costs that people don’t like to think about:
Estimates for engineering development costs are challenging, and I mean really challenging. The main reason is because something is being created from nothing, and there are a lot of components (software and hardware) that have to work together in harmony (protocols, algorithms, physical interfaces, power consumption, heat dissipation) in order for the embedded controller to perform as desired.
I think the majority of costs that engineers don’t like to think about are areas that are generally considered less fun, but that doesn’t make them any less valuable.
Embedded designers are more apt to want to focus on the creation aspect of the core design (e.g. coding on the software/firmware side, and circuit design on the hardware side), and less likely to want to pay as much attention to costs associated with tasks such as these 9 that I’ve identified below.
Cost 1: Requirements –
Many of the more formal methods for requirements generation and management may be overkill for some industries, and sometimes people get out of hand with requirements, but that’s not a good reason not to do anything at all. Consider developing a minimum set of requirements for your scenario.
Here’s why you should care: Requirements are the core of communicating what your industrial embedded system will become. Often the objective with requirements is getting one person to convey and organize information that’s in their head, with others. Developing and managing requirements isn’t free, but it can cost you even more by not paying attention to them. Not having requirements could create the need for a board re-spin, or could cause processor overloading. Requirements ultimately transform into what you design and test against. What you test against ultimately is what you judge success or failure against.
Cost 2: Project management –
Hardcore developers often hate project management, seeing it as superfluous. On the smallest of projects, project management can be handled individually. Otherwise, at a minimum, it’s a necessary evil.
Here’s why you should care: Project management can make the development team’s life better by helping you:
- not get overloaded
- clear roadblocks
- by providing clear goals.
Cost 3: Risk mitigation –
If nothing ever goes wrong with any of your projects, I’d be grateful if you’d get in touch with me and explain your magic. Otherwise, you should understand the likelihood and severity of your main risk items.
Here’s why you should care: Understanding your main risk items can help you come up with backup plans if a risk item occurs, and at a minimum, can be used as a tool to set expectations with the team, management, and your customer.
Cost 4: Documentation –
There are a few people out there that enjoy documenting. For the rest of us that don’t enjoy it, it’s worth noting that it can get out of hand. Just documenting because you’re supposed to, is not a very good reason in my mind. Keep it to a minimum.
Here’s why you should care: The three most helpful reasons to document in my mind are:
- to help you design in the first place
- to help teach someone else whatever they need to know
- to help you remember what you did a year or more later.
If none of these criteria are met, second-guess your effort.
Where you might head from here:
Check out part 2 of this article where we cover the other 5 costs that people don’t like to think about when designing an embedded controller. If you’d like more useful info on industrial embedded systems, check out our resources page. If you’d like help scoping the cost of your industrial embedded controller, you can reach out to us here.